WAM Products - Process Industry
WAMGROUP, WAM is the global market leader in Screw Conveyors and amongst the most prominent players in the field of Bulk Solids Handling & Processing Equipment. The company founded in Modena, Italy, in 1968, employs some 2,100 people at more than 60 locations in 40 countries. The Company’s comprehensive product range includes equipment for Bulk Solids Handling & Processing, Dust Filtration, Waste Water Treatment and Renewable Energy Generation. Strongly focused on the requirements of the market, WAMGROUP aims to produce market-oriented solutions turning them into a particularly user-friendly standard, tailored for a variety of industries. Industrial quality and an excellent price-performance ratio make WAMGROUP equipment the ideal choice for project engineers and provide customers all over the world with the best deal available on the market

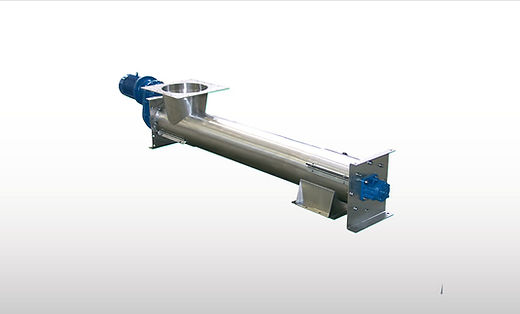
Stainless Steel Tubular Screw Conveyors-TX
TX Stainless Steel Tubular Screw Conveyors offer a variety of solutions for conveying or feeding powdery or granular materials. They are suitable for applications in which any contamination of the material handled has to be strictly avoided and where absolute cleanliness and perfect resistance to corrosion are required.
In particular, TX Tubular Screw Conveyors are used in environmental technology, in flour and animal feed milling, in food processing and packaging, in plastics and chemicals, as well as in the pharmaceutical industry.
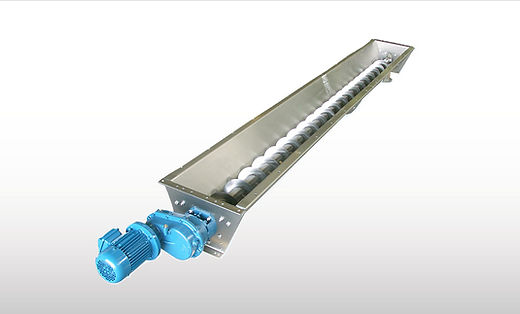
Stainless Steel Trough Screw Conveyors- CX
The modular CX Trough Screw Conveyor system offers a variety of solutions for conveying or feeding powdery or granular materials. Designed for application in the food industry and in environmental technology, they are suitable for applications in which any contamination of the material handled has to be strictly avoided and where absolute cleanliness and perfect resistance to corrosion are required. CX Trough Screw Conveyors are also used in flour and animal feed milling, in plastics and chemicals, as well as in the pharmaceutical industry.
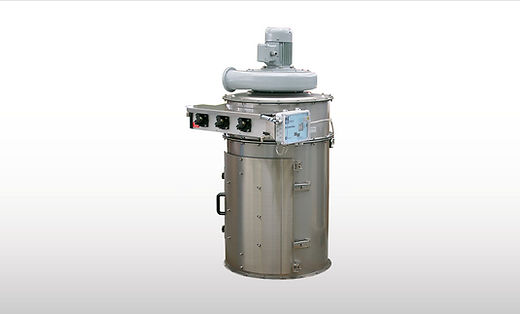
Flanged Round Dust Collectors -WAMFLO
The WAMFLO Dust Collector range is the result of WAM’s decades of experience in dust filtration technology. Since it went into production shortly after the turn of the millennium, tens of thousands of units have left the Group’s manufacturing plants all over the world. In diverse configurations WAMFLO has proved to be suitable for a variety of applications in virtually all industries.
WAMFLO Dust Collectors are equipped with a cylindrically shaped stainless steel body and flanged bottom ring which contains vertically mounted filter elements of various types including the high efficiency POLYPLEAT. An air jet filter element cleaning system is integrated in the hinged top cover. WAMFLO Dust Collectors are available with or without suction fan. As an option for applications with top-mounted suction fan or in case of limited headroom, WAMFLO can be equipped with a large front door which facilitates access to the filter elements in case of inspection or maintenance. In the food-grade version WAMFLO comes in a zero dust residue design. WAMFLO is supplied with an integrated modular electronic panel able to manage cleaning cycles according to the specific requirements of the work process. It is suitable for operation in explosive environments.

Bin Activators –BA
To fit the BA Bin Activator, the silo cone has to be shorter than usual, leaving a wide outlet section. A flange supplied before or together with the Bin Activator is welded on the silo outlet cone on site. Special suspensions and a seamless, flanged SINT engineering polymer seal form a flexible connection between silo and Bin Activator. One or two electric OLI motovibrators fitted on the unit generate vibration of the Bin Activator every time the feeding device beneath the silo is started for feeding material. During operation the Bin Activator describes a gyratory movement which is transmitted to the material inside the silo. The result is smooth material flow through the Bin Activator outlet into the connected feeder.
BA Bin Activators are used in various industrial applications to facilitate discharge of powdery or granular materials from a silo or hopper. The use of this equipment ensures optimum feeding of the material according to a “mass flow” condition, thus avoiding bridging or rat holing phenomena.
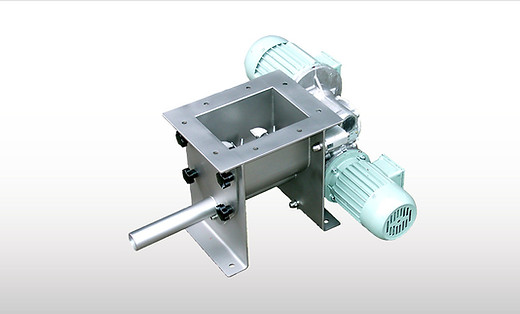
Micro-Batch Feeders with Agitator- MBF
The MBF Micro-Batch Feeder for continuous volumetric feeding of powdery or granular materials consists of a steel-reinforced SINT engineering polymer body (optionally body entirely manufactured from stainless steel), a horizontally mounted rotating agitator tool, a feeder screw beneath the agitator tool, a feeder pipe enclosing the protruding feeder screw, one drive unit each for agitator and feeder screw.
Tests on product flow and material stress were carried out to establish optimum body geometry. Agitator and feeder tool geometry and materials were tested, too, before choosing an optimal steel and SINT engineering polymer composite.
On request, MBF series Micro-Batch Feeders are supplied in food-grade versions with both FDA and EN- approval.
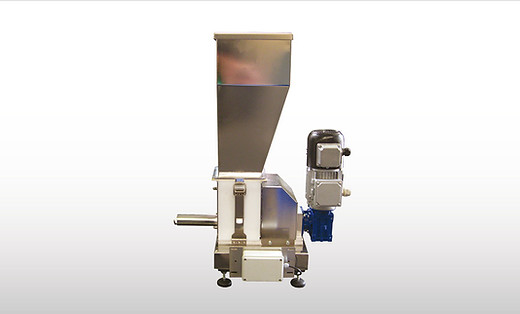
Loss-In-Weight Screw Feeders -DCC
DCC Loss-In-Weight Screw Feeders consist of a micro-screw feeder inside a food-grade polymer body with stainless steel guards and feeder pipe and an optional electronically operated scale pan mounted on load cells. Wherever powders or granular materials have to be continuously fed and metered, DCC-type Loss-In-Weight Screw Feeders offer exceptional operating versatility due to highly precise metering performance and excellent user-friendliness.

Drop-Through Rotary Valves –RVC
RVC Drop-Through Rotary Valves consist of a tubular cast iron or stainless steel casing, a horizontally mounted rotor with a certain number of oblique V-shaped cross section compartments, a drive unit and casing covers at both ends. Two compartments at a time of the continuously turning rotor are filled up with material entering through the inlet at the top of the Rotary Valve. After less than half a turn material falls through the bottom outlet opening having the same cross section as the opposite inlet.

Blow-Through Rotary Valves-RVS
RVS Blow-Through Rotary Valves consist of a tubular cast iron or stainless steel casing, a horizontally mounted rotor with a certain number of oblique V-shaped cross section compartments, a drive unit and a casing cover at each end. Two compartments at a time of the continuously turning rotor are filled up with material entering through the inlet at the top of the Rotary Valve. After less than half a turn material falls through the bottom outlet into an air stream passing through a pneumatic conveying pipeline connected with the bottom part of the Rotary Valve.

Slide Valves -VL
VL-type Slide Valves consist of a two-piece carbon or stainless steel frame partly coated with WAM’s SINT engineering polymer composite, as well as a sliding blade manufactured from SINT engineering polymer, carbon steel or stainless steel. The use of the unique SINT engineering polymer composites considerably increases resistance to abrasion as compared to traditional valves. Moreover, it avoids the use of flange gaskets.
VL Slide Valves are available in a variety of configurations including rectangular sizes. In the VLQ version the valves come with a square, in the VLC version with a circular open cross section, whereas in the VLR-version it is rectangular. The VLS version with square cross section has a pneumatic actuator integrated in its frame.

Pinch Valves -VM - VMM
The body of the VM/VMM Pinch Valve is manufactured from aluminium alloy while the sleeves come in fabric-reinforced material. The sleeve support bushes are either made from aluminium alloy, hardened carbon steel, or 304/316 stainless steel. VM and VMM-type Pinch Valves are used for interception of material flow in pneumatic conveying systems, or other pipelines. In addition, they can be installed as a locking device for silo filling pipes.
Regarding VM only, by introducing compressed air through the threaded bore into the interior of the valve, the internal flexible sleeve is reshaped in such a way as to hermetically seal the passage. With VM Pinch Valves pneumatically conveyed powders, granules, fibres, dense mixtures and liquids can be equally handled.
Regarding VMM only, by introducing compressed air into the two single action air cylinders, the internal flexible sleeve is kept open. In case of no presence of air, the cylinders will reshape the sleeve in such a way that the passage is hermetically sealed. VMM Pinch Valves can equally handle pneumatically conveyed powders, granules, fibres, dense mixtures or liquids.

Diverter Valves for Pneumatic Conveying Lines –VAD
AD Diverter Valves consist of an aluminium die-cast casing and a swivel flap that closes one duct or the other. Internal sealing of the body is achieved through low friction gaskets.
Specific surface treatment is available to make the valves suitable for operation with different materials.
VAD-type Diverter Valves are suitable for use in pneumatic conveying lines for handling any type of material in powdery or granular form.
Through activation of the actuator direction of the material flow is changed. VAD-type Diverter Valves guarantee minimum pressure loss and contamination-free, pressure-proof operation.

Drum-Type Diverter Valves for Pneumatic Conveying -VAR
VAR Diverter Valves consist of a cast aluminium casing and cover, an inlet and two outlets. The rotating internal drum optionally closes one of two outlets which are connected with pneumatic conveying ducts.
Rotation of the internal drum is activated by a pneumatic actuator.
Perfect sealing is guaranteed by internal, pneumatically inflatable seals. VAR Diverter Valves are suitable for diverting or converting any type of powdery or granular material.
Commutation of the tubular exit and diversion of the material flow from one duct to another is obtained by a pneumatic actuator which activates the rotating inner drum.

Flap Diverter Valves -VAB
The VAB Flap Diverter Valve uses a swinging flap to divert material from one duct to another.
VAB Flap Diverter Valves are fitted on pneumatic conveying ducts in which switching the flow of material to different production lines is required. The VAB Two-Way Flap Type Diverter Valve is designed to meet the requirement of pneumatic conveying plants in re-routing powders, pellets or granules from one discharge point to another, with minimum pressure drop and high sealing efficiency.

Diverter Flap Valves- DVA
DVA-type Diverter Flap Valves consist of a casing made up of two high-pressure die-cast semi-bodies manufactured from aluminium alloy, lined with SINT engineering polymer, and a SINT engineering polymer flap. The flap is either activated by a manual lever, a pneumatic or an electric actuator. DVA is a Diverter Flap Valve with one inlet and two outlets for the diversion of the flow of powdery or granular materials. Materials used enable quick cleaning and maintenance apart from offering great resistance to abrasion.

FIBC Filling Systems -RBB
RBB-type FIBC Filling Stations consist of a steel frame and a bag filling unit including an inflatable seal that impedes dust leakage during filling. RBB-type FIBC Filling Stations enable efficient filling of bulk bags. The empty FIBC is attached to the four stretchers in the upper corners of the frame. Then the bag inlet is pulled over the loading spout of the station. Filling starts as soon as the seal around the bag inlet is inflated. Once the FIBC is filled up it is lifted by a forklift truck, removed from the steel frame and transferred to its further destination.

Lump Breakers- DLP
The DLP Lump Breaker consists of a square cross section casing with upper and lower flange, two horizontal rotating shafts equipped with chopping knives, a grid to hold back lumps, four end bearing assemblies with integrated adjustable shaft seal, an appropriately sized drive unit complete with power transmission. The DLP Lump Breaker is the ideal device for breaking up material lumps which have formed during handling or processing but are soft enough to be broken up.
Quick rotation of special chopping knives through a fixed grid does the job. The presence of two rotor shafts results in high throughput rates.

Tanker Loading Bellows With Integrated Dust Collector -BELLOJET ZA
BELLOJET ZA Loading Bellows are used for efficient, dust-controlled loading of dry, dusty bulk solids into tankers. The spouts are provided with inner tapered cones to contain the flow of material and an outer double bellows to provide for dust removal. At the lower end of the Loading Bellows, a SINT engineering polymer-coated cone with special sealing properties is provided for connection to the tanker.
First the Loading Bellows is lowered from stand-by position towards the inlet spout of the tanker. As soon as the bellows outlet cone settles on the inlet spout of the tanker, the slack cable switch mounted outside the transmission box stops lowering of the bellows. The limit switch inside the transmission box stops both full extension and contraction of the bellows. Material loading is started by opening the silo outlet valve.
During filling of the tanker, the polymer coating of the outlet cone acts as a perfect dust seal. At the same time the filter fan continuously sucks dust through the external bellows into the integrated filter cartridges in the upper section of the unit exhausting excess air. A slack cable switch activates further extension of the bellows as the tanker lowers under the increasing material weight. A level monitoring device installed in the centre of the outlet cone signals maximum material level in the tanker compartment and orders immediate closing of the silo outlet valve. Contraction of the bellows back to stand-by position starts after a delay of approximately ten seconds in order to allow the filter to evacuate the remaining dust. Once the bellows is fully contracted, the cable limit switch inside the transmission box stops operation. The preset after shut-down cleaning cycle now provides for additional pulse-jet cleaning of the filter cartridges for another ten minutes.

Continuous Single Shaft Mixers -WAH
WAH Continuous Horizontal Single Shaft Mixers consist of a cylindrical mixing drum vessel with an inlet at one end of the mixing drum, an outlet at the opposite end and a venting spout, a full material mixing shaft, two drum closing end plates that carry flanged end bearing assemblies complete with integrated air or gas-purged shaft seals, and a drive unit complete with power transmission.
Ploughshares or inclined blade-type shovels rotate as mixing tools in a special arrangement on the mixer shaft inside the drum vessel. The result is a turbulence in the mix that constantly involves all the product particles in the mixing process. The formation of dead spots or slow-movement zones in the mixing drum is prevented ensuring precise mixing. In some cases, to obtain the desired mixing effect, separately driven high-speed choppers can be installed.

Batch-Type Single Shaft Mixers- WBH
WBH Horizontal Single Shaft Batch Mixers consist of a mixing drum vessel with an inlet, an outlet with discharge valve and a venting spout, a full material mixing shaft, two drum closing end plates that carry flanged end bearing assemblies complete with integrated air or gas-purged shaft seals, and a drive unit complete with power transmission.
Ploughshare or inclined blade-type shovel tools rotate as mixing tools in a special arrangement on the mixer shaft in a horizontal, cylindrical drum vessel. The result is a turbulence in the mix that constantly involves all the product particles in the mixing process. The formation of dead spots or slow-movement zones in the mixing drum is prevented ensuring precise mixing. In some cases, to obtain the desired mixing effect, separately driven high-speed choppers can be installed.

Tubular Batch-Type Ribbon Blenders- WBN
Batch-type WBN Ribbon Blenders consist of a horizontal, single shaft double counter-pitch ribbon screw housed in a tubular mixing drum, a central inlet or a rectangular shape inlet port over the entire length of the mixing drum, an outlet with central discharge outlet, a venting spout, two drum closing end plates complete with integrated air or gas-purged shaft seals, and a drive unit complete with power transmission.
The outer helix moves the material from both ends of the vessel towards the centre, while the inner helix transfers the material towards both ends, performing a sort of convective mixing. The product is gently processed in a relatively short mixing time.
Typically Batch-type WBN Ribbon Blenders are used for mixing dry PVC, dry powders or granules in general, as well as liquids and low-viscosity pastes.

Continuous Twin Shaft Paddle Mixers- MESC-MESC-UM
MESC-type Twin Shaft Paddle Mixers (MESC-UM with liquid injection as conditioner) are equipped with two parallel counter-rotating, intermeshing paddle shafts. The adjustable angle of inclination of the mixing paddles allows perfect adaptation to different material characteristics and mixing process requirements.
MESC-type Twin Shaft Paddle Mixers are used for powder mixing, sludge granulation and neutralisation, as well as for dust, ash, or sludge conditioning.

Dust Conditioners- DUSTFIX
The DUSTFIX Dust Conditioner consists of a carbon steel tubular housing with SINT engineering polymer liner, a combined feeder screw/mixing shaft, one vertical inlet and a SINT flush outlet, a liquid supply point in the conditioning section, and a drive unit with integrated shaft seal.
The DUSTFIX Dust Conditioner is the ideal machine for the evacuation, conditioning and disposal of industrial dusts in terms of function and economy. Due to its particular technical features, the use of innovative SINT engineering polymers and extremely short processing time, DUSTFIX is suitable for continuous duty.

Bin Level Indicators- ILV
ILV-type Bin Level Indicators are designed for electric signalling by fork vibration of minimum or maximum material level inside bins, hoppers or silos. The ILV device is used for level monitoring in all types of bins or silos and for all kinds of powders or granular materials.